Induction Heating aluminium susceptor
Views Send Enquiry
Objective Expand powder into solid form for use in crash helmets
Material Microspheric powder
Aluminium chamber 110mm (4.3 in.) diameter x 35mm (1.3 in.) deep used to hold powder
Temperature 150 oC (302 oF)
Frequency 54.5 kHz
Process Time 20 seconds
Equipment . Power of 35 kW induction heating system, equipped with a remote workhead containing (4) 2.6 ƒÊF capacitors (for a total of 2.6 ƒÊF).
. Two pancake coils 110mm (4.3 in) dia. with 45mm (1.8 in.) gap, in a headphone configuration designed and developed specifically for this application.
Process The bottom of the susceptor chamber is sprayed with a release agent and microspheric powder is added to the chamber. The chamber is heated for 120 seconds to reach 150o C (302o F) changing the powder into solid form. It is then allowed to air cool to 70o C (158o F) and removed from the chamber.
Results/Benefits Induction heating:
. reduces cycle time for increased production
. energy efficient – only heating the part allowing small production runs
. is very flexible allowing a variety of molds to be used
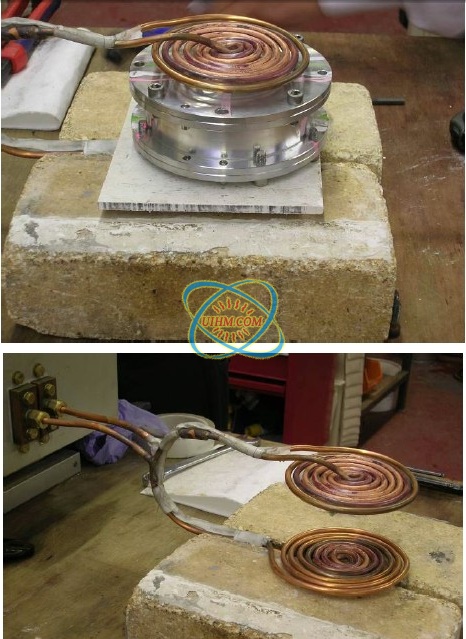
Heating aluminium susceptor
Related Content
induction brazing SS steel by handheld induction coil
induction melting silicon and steel
magnesium oxide acidic furnace for induction melting glass
induction preheating gas pipeline by full air cooled clamp induction coil and DSP induction heater
induction melting with Titanium alloy pot by customized induction coil
induction melting aluminium for casting wire wheel
induction heating steel plate by pancake induction coil
induction heating steel knife
Hot
induction painting after induction bending for pipelines
induction heating steel plate
induction remove copper from aluminium
induction heating stator frame
induction heating graphite mould
difference between induction heating inner surface and outside surface of steel ring
induction heating steel pot bottom
induction heating for heat preservation
Newest Comment
No Comment
Post Comment